Digital Twins
Digital Twins are progressively making their mark in the Architecture, Engineering, and Construction (AEC) industry. A digital twin can be defined as a virtual representation of a building, capturing real-world data about its structure through sensors, drones, and other wireless technologies.
This digital twin concept is often referred to as the integration of Building Information Modeling (BIM) and the Internet of Things (IoT). BIM enables architects, engineers, and contractors to collaboratively plan, design, construct, and manage a building's physical and functional attributes using 3D models. IoT, on the other hand, encompasses devices and sensors with embedded wireless connectivity, strategically placed within the built environment to extract real-time data, providing critical insights into the performance of various components.
- BIM-IoT Integration: The convergence of BIM and IoT is at the core of digital twins. BIM provides a detailed 3D model of a building's design, while IoT encompasses the deployment of sensors and devices that collect real-time data about the physical structure's performance and conditions. This integration allows for a more comprehensive understanding of the building's behavior and functionality.
- Collaborative Planning and Management: BIM allows architects, engineers, contractors, and other stakeholders to collaboratively plan, design, and manage various aspects of a building project. Digital twins take this collaboration a step further by enabling real-time monitoring and feedback throughout the building's lifecycle.
- Real-time Data: IoT sensors embedded in the building collect data on various parameters such as temperature, humidity, occupancy, energy usage, and equipment health. This real-time data is fed into the digital twin, providing an up-to-date and accurate representation of the building's current state.
- Advanced Analytics and AI: Digital twins leverage advanced analytics, artificial intelligence (AI), and machine learning algorithms to process the vast amount of data generated by IoT sensors. This enables predictive maintenance, energy optimization, and the identification of potential issues before they become critical problems.
- Facility Management: One of the primary applications of digital twins is in facility management. Facility managers can use graphical BIM models linked to IoT data to monitor and optimize energy usage, track service requests, and receive alerts for preventative maintenance. This proactive approach helps in prolonging the lifespan of building systems and reducing operational costs.
- Continuous Learning and Improvement: Digital twins are not static models but continuously learn and evolve. They adapt to changes in the physical environment and use historical data to improve their predictions and insights over time.
The digital twin continually learns from diverse sources, incorporating advanced analytics, artificial intelligence (AI), and machine learning algorithms to gain invaluable insights into a project's performance, operation, and profitability, whether it's already built or still under construction.
Benefits:
The use of digital twins in the AEC industry offers several benefits, including
- improved design accuracy,
- reduced construction errors,
- optimized building performance,
- energy efficiency,
- cost savings,
- enhanced facility management.
Digital twins represent a powerful fusion of BIM and IoT technologies that revolutionize the AEC industry. They provide a comprehensive and data-driven approach to building design, construction, and management, ultimately leading to more efficient and sustainable built environments.
AR, VR & MR
The adoption of Virtual Reality (VR) technology within construction projects is increasingly prevalent. This innovation allows individuals to take virtual tours of the planned structures, offering a glimpse of their final appearance once construction is completed. VR serves as a valuable tool for enhancing project comprehension among all stakeholders, including clients, contractors, subcontractors, and more. Recent advancements in VR have shifted from cumbersome headsets to the convenience of using smartphones for immersive experiences, indicating substantial future growth for this technology.
Augmented Reality (AR) entails integrating digital information into the physical environment. The utility of AR in construction is multifaceted, with capabilities such as illustrating the intricate MEP (Mechanical, Electrical, and Plumbing) installations within existing buildings. AR can elucidate how pipes run through walls or roofs, as well as provide insights into the appearance of structural fabrications at specific locations.
Mixed Reality (MR) represents a fusion of Virtual Reality (VR) and Augmented Reality (AR). This amalgamation seamlessly embeds virtual elements within the real world, akin to holographic integration.
The implementation of these technologies allows building owners to venture onto their construction sites, don their MR glasses, and explore their yet-to-be-constructed assets at a full-scale level. Observers can visualize potential alterations, zoom in on architectural details, and even step inside the building to gain a comprehensive pre-construction experience. This includes assessing various views from windows, evaluating the impact of relocating walls on room ambiance, and much more. Such technological advancements are poised to significantly benefit the construction and installation industries.
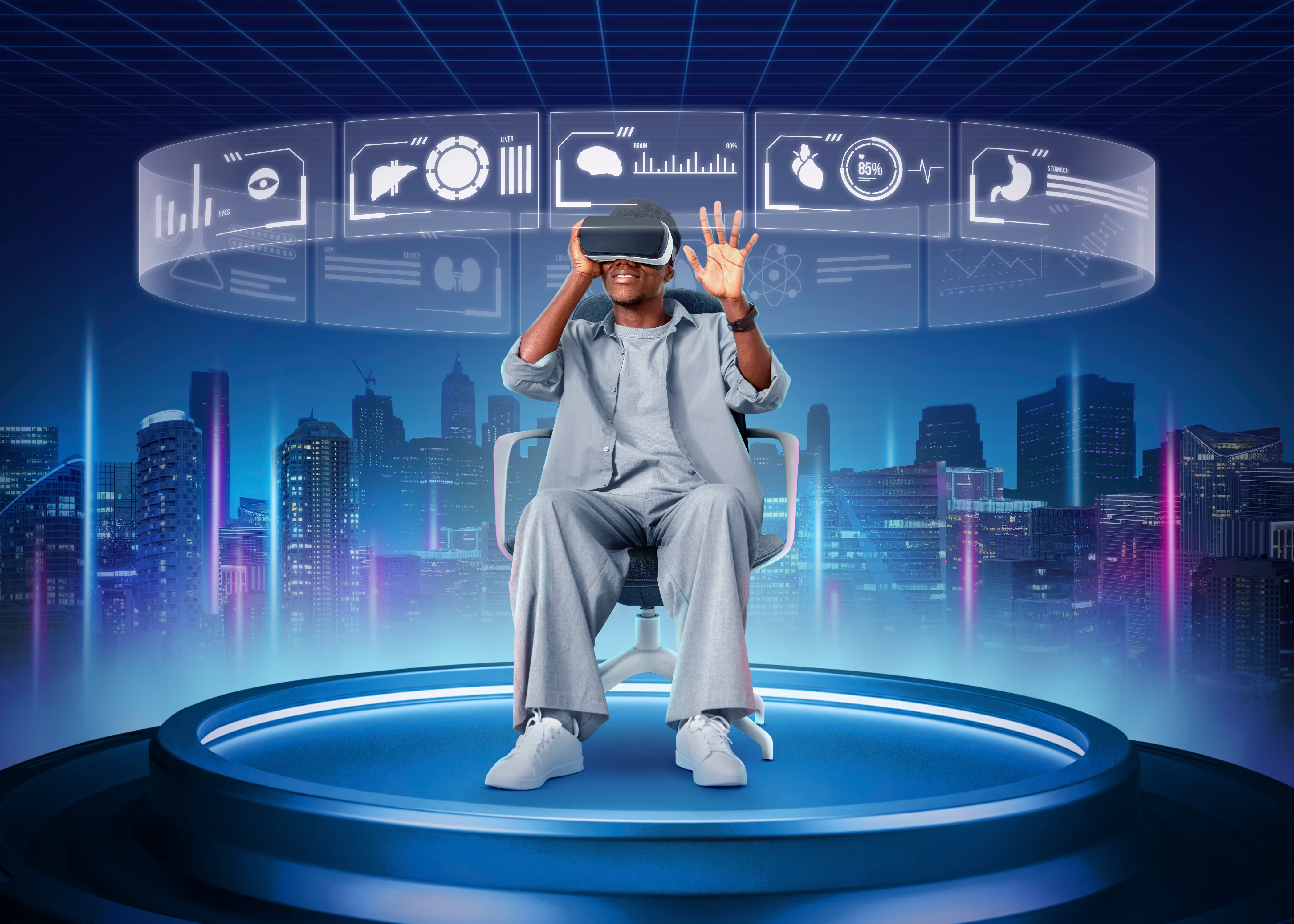
The integration of Virtual Reality (VR), Augmented Reality (AR), and Mixed Reality (MR) technologies in construction projects is indeed revolutionizing the industry in several ways:
- Enhanced Visualization: VR allows stakeholders, including clients, contractors, and subcontractors, to immerse themselves in a virtual representation of the project. This immersive experience enables a better understanding of the design, layout, and spatial relationships, which can lead to improved decision-making and design validation.
- Remote Collaboration: VR can facilitate collaboration among geographically dispersed teams. With the right VR equipment and software, project participants can meet in a virtual environment to discuss plans, make changes, and resolve issues without the need for physical presence.
- Cost and Time Savings: By identifying design flaws and potential issues early in the virtual stage, costly changes and delays during actual construction can be minimized. This can lead to cost savings and reduced project timelines.
- Client Engagement: Clients can have a more interactive and immersive experience when viewing and understanding the project. This can lead to increased client satisfaction and confidence in the project's outcomes.
- Safety Training: VR can be used for safety training and simulations, allowing workers to practice safety procedures and hazardous situations in a controlled virtual environment before encountering them on the construction site.
- Progress Monitoring: AR can be employed to overlay digital information on the physical construction site. This can assist in tracking progress, comparing it to the project schedule, and identifying any deviations or discrepancies.
- Maintenance and Operations: MR technology can be particularly valuable for building owners and facility managers. They can use MR glasses to inspect and visualize maintenance needs, access digital manuals or information, and make informed decisions regarding the building's ongoing operation.
- Design Iteration: VR and MR technologies make it easier to explore design variations and iterations in real-time. Architects and designers can make changes on the fly and immediately see the impact on the overall project.
- Improved Communication: The immersive nature of VR and AR can simplify complex technical information, making it easier for non-technical stakeholders to grasp critical project details.
- Quality Control: VR and AR can assist in quality control by allowing inspectors to overlay design specifications onto the physical construction, ensuring that it matches the intended design.
While these technologies are indeed promising and have the potential to transform the construction industry, it's essential to consider factors such as cost, hardware requirements, training needs, and data security when implementing VR, AR, or MR in construction projects. Additionally, as technology continues to advance, we can expect even more innovative applications in the construction sector, further enhancing productivity and efficiency.
Generative Design
Generative design represents a revolutionary paradigm shift in the realm of digital engineering. It emulates the evolutionary principles of design, encapsulating all the essential attributes. When coupled with cutting-edge high-performance computing and cloud technologies, it empowers engineers with capabilities they could only dream of.
Generative design leverages artificial intelligence and machine learning (AI & ML) to replicate a design process akin to nature's own. It interfaces with engineers by accepting input parameters to yield a desired outcome.
The advent of practical artificial intelligence (AI) algorithms has propelled generative design tools into the mainstream. This means engineers can now generate thousands of design alternatives seamlessly integrated into their digital designs, selecting the one that best aligns with their requirements.
Whether dealing with specific load placements, material thickness constraints, or cost considerations, generative design tools can take all these data points into account. Once the program runs and the algorithms do their work, engineers receive generative designs that adhere to their input criteria. They can then peruse multiple options and choose a design that optimally serves their objectives, customizing it as needed. In essence, it provides a digital shortcut to achieving the ideal design according to specified criteria.
Advantages:
The advantages of generative design are manifold.
- accelerates the design process,
- reduces manual effort,
- can lead to more sustainable and cost-effective solutions.
- empowers architects, engineers, and designers to focus on creativity and problem-solving rather than labor-intensive design tasks.

- Mimicking Nature: Generative design draws inspiration from nature's evolutionary approach to design. It uses artificial intelligence and machine learning to replicate this process digitally. By doing so, it can generate a wide range of design options that may not have been explored using traditional design methods.
- Input-Driven: Engineers can input specific design parameters and constraints into generative design tools. These constraints can include factors like loads in specific locations, material thickness requirements, cost limitations, and more. The software then uses these inputs to generate designs that meet the specified criteria.
- Algorithmic Optimization: Generative design relies on complex algorithms to explore a vast design space. It iterates through numerous possibilities to find designs that are both feasible and optimized. This not only saves time but also leads to innovative and efficient designs.
- Design Exploration: Engineers are presented with multiple design options generated by the software. They can evaluate and compare these designs to select the one that best aligns with their project's goals. This process enables rapid exploration of design alternatives.
- Integration with Software: Generative design functionality is being integrated into various design and engineering software tools. Autodesk Revit, as you mentioned, is one example of software that has incorporated generative design capabilities, making it more accessible to professionals in the architecture, engineering, and construction (AEC) industry.
- Future Potential: With the continuous growth of artificial intelligence, machine learning, and automation technologies, generative design is poised to become increasingly influential in various industries, including BIM (Building Information Modeling). It can help streamline workflows, improve design quality, and drive innovation.
Notably, Autodesk Revit 2021 (AEC Collection) has recently integrated Generative Design functionality, marking a significant milestone. Generative design is poised to play a pivotal role as we advance into the future. In tandem with the growth of artificial intelligence, machine learning, design automation, and other technologies, it is destined to be a game-changer in the BIM industry!
Cloud Collaboration
Cloud technology plays a pivotal role in facilitating collaborative BIM-based efforts among various stakeholders and interdisciplinary teams involved in intricate AEC projects.
The onset of the Covid-19 pandemic compelled businesses to embrace remote work strategies, leading to a profound realization of the potential of cloud technology. While this shift posed challenges to the AEC industry, it remarkably adapted. Geographically dispersed technical teams swiftly embraced cloud services to ensure uninterrupted collaboration on their BIM projects.
Even Common Data Environments (CDEs) have found a new home in the cloud, granting all employees access to the most up-to-date BIM data relevant to their projects. One exemplary platform is CUBE, a cloud-based software lauded as the next-generation BIM management solution. Every team member gains access to the latest BIM data and can securely store essential BIM documents such as BIM Execution Plans (BEPs) and Exchange Information Requirements (EIRs) in the cloud. Additionally, a 3D viewer facilitates direct BIM file viewing on the cloud.
.avif)
- Adaptation to Remote Work: The COVID-19 pandemic forced companies in the AEC industry to adapt to remote work strategies, highlighting the importance of cloud technology. This shift allowed teams to collaborate effectively even when dispersed worldwide.
- Cloud-Based Common Data Environments (CDEs): Common data environments, a critical component of BIM workflows, are now being hosted on the cloud. This provides employees with easy access to the latest BIM data related to their projects.
- Examples of Cloud-Based BIM Platforms: Such platforms offer features like access to the latest BIM data, storage for BIM documents, and 3D viewers for viewing BIM files directly in the cloud.
- Role of 5G: The deployment of 5G services by the telecom sector is contributing to high-speed internet access, which further accelerates the adoption of cloud services for BIM collaboration and management. Faster internet speeds are crucial for handling large BIM data sets.
Moreover, the widespread deployment of 5G services by the global telecom sector is democratizing high-speed internet access, further expediting the adoption of cloud services and platforms for BIM collaboration and management in the foreseeable future.